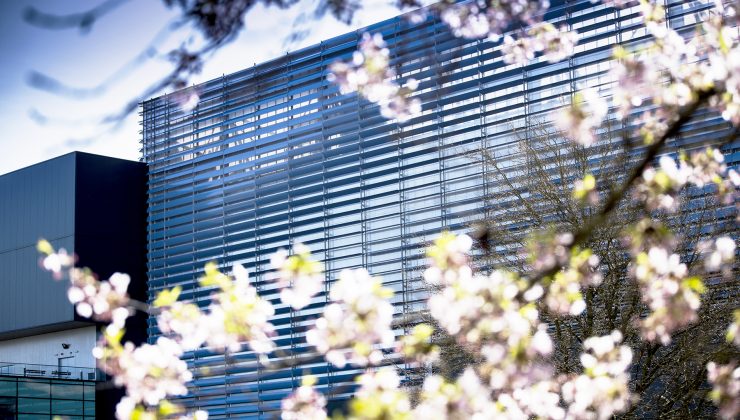
Reception hall
A large reception hall allows waste vehicles to tip waste safely. Air needed for the combustion process is drawn into the furnace from here, so that odour and dust are contained within the building.
Bunker
Waste vehicles tip their loads into a large concrete bunker, big enough to hold six days worth of waste.
Control room
All of the facility’s equipment, including the grabber which mixes the waste in the bunker, is operated from the control room. Control systems check that equipment is working properly, continuously monitor the combustion gas and make sure the whole facility is working to maximum efficiency. Everything is monitored both automatically and manually.
Grate and boiler
Air is blown into the bottom of the water‑cooled grate through five computer‑controlled zones. The heat released from burning the waste is used to convert water to super‑heated steam. At high pressure, this steam drives a turbine to generate electricity.
Air-cooled condensers
After leaving the turbine, the steam goes through an air-cooled condenser and is condensed back to water, which is then treated and reused in the boiler to produce more steam. This closed‑loop system minimises the amount of water needed.
Emission control
Control of emissions starts in the furnace with good combustion control to make sure the correct proportion of air is supplied and temperature is maintained.
Combustion gases from the furnace are subject to a rigorous cleaning process. Nearly one-third of the facility is taken up with the cleaning process, which involves spraying activated carbon and lime into the flue gasses to neutralise any pollutants.
Monitors at the base of the chimney continuously check emission levels and if they start to rise, adjustments are made to the cleaning process. In the unlikely event they continue to rise, or if the monitoring equipment fails, the facility will automatically shut down.
Monitoring information from the chimney is displayed both in the visitor centre and on our website, on the emissions monitoring page. It is also sent to the Environment Agency.
Air pollution control residue
The cleaned gas is passed through fine-fabric bag filters to remove solid particles. The resultant air pollution control residue (also known as fly ash) contains these solid particles, excess lime, salts and carbon dust.
This is taken away from site in sealed containers for specialist landfill. It is hoped in the future it will be used for low-carbon building blocks.
Bottom ash
Ash left on the grate after incineration is cooled and carried along a conveyor to an on-site processing building. Metals are removed from the ash for recycling. The remaining aggregate is graded according to size and sent for use in building projects. The aggregate is commonly used to construct road surfaces.
Electricity
Electricity is generated at 11 kilovolts. Around three megawatts is used to power the facility, leaving around 20 megawatts, which travels along an underground cable to a sub-station in Stowmarket, where it is fed into the National Grid.
Heat
The facility is also capable of producing up to 15 megawatts of heat. Supplying heat to nearby premises would reduce the electricity output, but would make the facility even more efficient at getting the most from the waste.
Servicing and maintenance
Servicing and maintenance of the facility takes place annually, when the facility is shut down. Maintenance work on the two identical incineration lines is staggered, so that waste can continue to come into the facility and the length of time the facility is shut down is limited.